全国高级能源管理高级能源审计 节能评估 合同能源管理 碳排放 碳中和 碳达峰 碳交易 碳资产管理 等知识培训详细了解
《高级能源管理》《高级能源审计》《碳资产管理》证书考取
2024年4月26日-28日 线上学习
30项绿色节能低碳环保技术分析
本文按照以下目录分类整理最新绿色节能低碳技术:
一、绿色节能减碳技术
二、余热高效利用技术
三、高温烟气除尘技术
四、烟气高效除尘技术
五、脱硫脱硝技术
01
一、绿色节能减碳技术

01移动床 VOCs 治理及溶剂回收一体化技术(1)移动床VOCS治理及溶剂回收一体化技术介绍以碳基功能材料为核心,集合连续多通道轴径向吸附、清洁高效吸附材料解析-回收等关键技术,实现VOCs治理关键技术集成,不仅可无害化处理VOCs污染,又能绿色安全地将VOCs富集捕获并资源化,该技术可应用于化工、钢铁、焦化、医药防护、橡胶等行业VOCs治理。
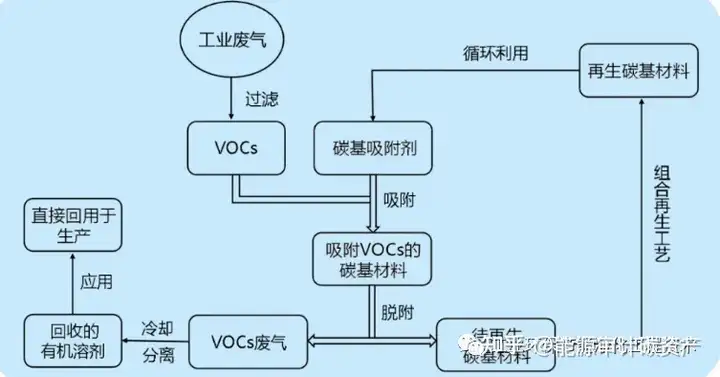
(2)工艺优势
1)物理吸附,常温常压操作,安全性能优越;
2)适用范围广,抗负荷冲击能力强;
3)多级吸附,VOCs出口浓度可稳定控制在20mg/m³以下,实现超低排放;
4)处理效率高达99%以上;
5)床层阻力小,吸附效率高,热能利用率高,运行能耗低;
6)专利吸附床设计,解决了传统固定吸附床板结及偏流的问题;
7)溶剂回收率高,品质好,可直接回用;
8)资源回收有收益,投资回报率高;
9)实现二氧化碳的减排,助力碳达峰、碳中和;
10)打造“双循环”经济,企业实现溶剂和吸附材料的循环。(3)产品型号及吸附剂材质
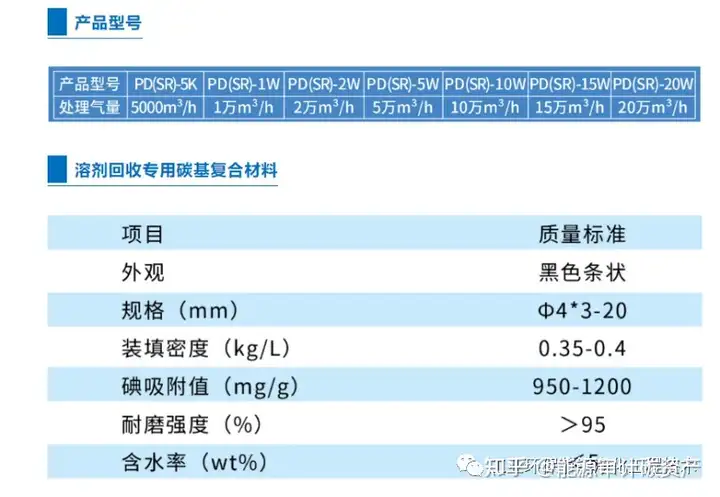
针对各行业的VOCs成分特性及客户需求,定制不同孔径分布的碳基复合材料,通过表面改性处理,提高材料的工作容量及强度,增强吸附脱附速度和吸附稳定性,实现材料的反复再生,延长使用寿命。(4)该装置还可根据废气特性选择相应的吸附剂,实现脱除H2S、苯、萘、氯、VOCS等气体的功能。①PCT型改性活性炭脱硫剂主要应用于合成氨、天然气、焦炉煤气、城市煤气、发电厂等气体中H2S预处理。②PCT-06活性炭吸油剂主要用于合成氨、二氧化碳、压缩机后的油污、焦炉煤气、天然气中苯、萘的脱除及煤制油原料气体中的净化。③PCT-03 转化吸收活性炭精脱硫剂主要应用于煤制合成氨、天然气、焦炉煤气、水煤气、二氧化碳、尿素合成气中H2S及COS 、CS2、硫醇、硫醚等有机硫转化吸收。④PCT-11 活性炭脱苯剂主要应用于各种工业气体如焦炉煤气、天然气等气体中苯的脱除。⑤PCT-09 活性炭脱萘剂主要应用于合成氨、天然气、焦炉煤气、城市煤气、发电厂等气体中萘的处理。⑥PZT-02 中温(高温)氧化锌脱硫剂主要应用于生产甲醇、合成天然气、焦炉煤气、合成氨、石油化工干气、精细化工气相脱除H2S和柴/汽油、润滑油装置脱除H2S。⑦PCT-04A型 常温脱氯剂主要应用于合成氨、合成天然气、焦炉煤气、天然气及石油化工中循环氢中HCI的脱除。⑧PS-02型 宽温有机硫水解剂主要应用于合成氨精脱硫工段和尿素合成工段、煤制天然气、焦炉煤气制天然气、食品级二氧化碳、聚丙烯等原料气常温下的COS转化。

02工业烟气CO脱除技术(1)CO脱除的意义 我国大气环境质量主要监测指标有PM10、PM2.5、臭氧、二氧化硫、氮氧化物和一氧化碳六大项,随着近年来各行业超低排放治理的快速推动,二氧化硫、氮氧化物和粉尘等治理已经接近尾声,但是CO的治理由于技术不成熟的原因,一直没有开展。 工业烟气脱除CO具有重大意义,一方面,CO在极低浓度时能使人或动物遭到缺氧性伤害,轻者眩晕、头疼,重者脑细胞受到永久性损伤,甚至窒息死亡等危害;另一方面,CO主要为燃料燃烧不完全产生的,CO的排放本身就是对能源的一种巨大浪费,经计算,如果将工业烟气中每1%(即10000PPM)的CO催化氧化为CO2,释放的热量可将烟气温度提升约60℃,以干熄焦常用放散烟气为例,烟气中CO含量通常≤6%,如将烟气中CO脱除,催化氧化为CO2,则可将烟气温度提升360℃,实现对烟气余热的回收,从而提高能源的利用率,减少对化石能源的消耗,到达节能与减碳的目的。(2)CO催化氧化原理
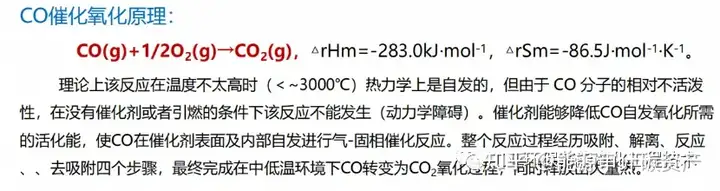
催化燃烧反应原理是有机废气在较低温度下在催化剂的作用下被完全氧化和分解,达到净化气体目的。催化燃烧是典型的气固相催化反应,其原理是活性氧参与深度氧化作用。在催化燃烧过程中,催化剂的作用是降低反应的活化能,同时使反应物分子富集在催化剂表面上以提高反应速率。借助于催化剂,有机废气可以在较低的起燃温度下无焰燃烧并且在释放大量热量,同时氧化分解成CO2和H2O。CO在150℃就会发生催化氧化反应,250℃条件下脱除效率可达90%。
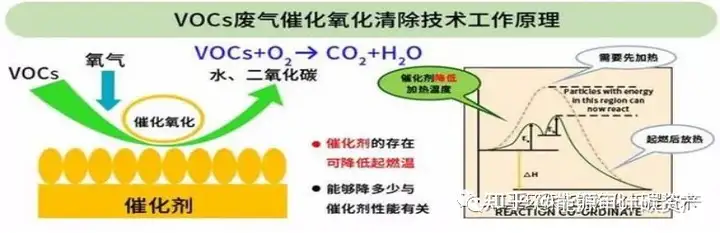
(3)催化剂影响因素 由于钢铁等工业锅炉烟气成分复杂,尤其烟气中的水分、粉尘(化学成分含碱金属和碱土金素)、SO2和烟气温度,都对脱一氧化碳催化剂的使用造成影响。按照现有的技术,烟气经过脱硫和除尘后,颗粒物和碱金属含量会大幅降低,但是烟气中仍然会存在少量 SO2(30 mg/m3),此外还有未处理的水分和 VOCs 等。SO2 容易和大部分金属氧化物反应形成硫酸盐从而使催化剂发生硫中毒失活;水会对部分催化剂的 CO 氧化过程产生抑制作用;VOCs等有机物会在催化剂表面发生不完全氧化,形成积碳,会导致催化剂活性持续降低。抗中毒催化剂的开发将是未来 CO 催化剂工业应用需要重点关注的问题。(4)催化剂的技术参数即特性区别于普通的催化剂结构,采用核壳结构催化剂,在活性物质外围包裹保护壳,选择性隔离有害物质,提升催化剂的耐水、耐碱金属、耐硫特性,降低对烟气洁净度的要求,增大使用范围。
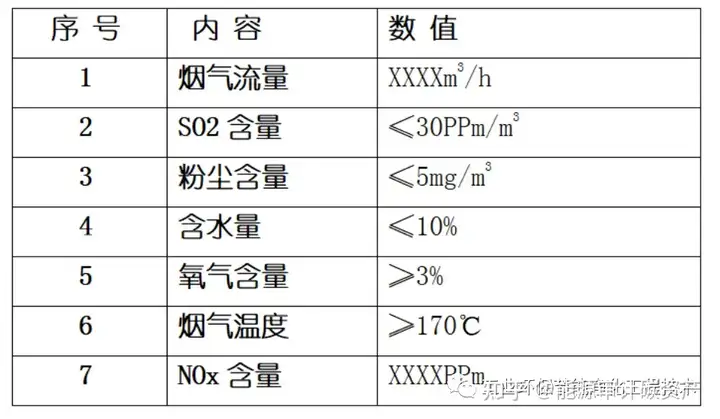
较低的CO起燃温度特性:由于烟气温度较低,需开发出较低的CO起燃温度特性的催化剂,我公司开发出的CO催化剂(钢铁、工业锅炉),T50≤130℃、T90≤140℃,从而完全满足催化剂应用条件; 较宽催化剂适用温度:我公司可根据不同的烟气条件,燃料种类,合理的空速特性开发满足150-500℃的脱CO催化剂。 高转化率特性:公司自研技术,转化率能到达95%以上; 寿命长特性:试验证明,脱一氧化碳催化剂衰退慢、寿命可长达24000小时。

03转炉喷煤减碳技术(1)转炉煤气回收的技术背景
转炉冶炼前期和后期,由于炉气中氧气含量超标,无法回收,只好放散。虽然采取了点燃措施,但是由于煤气热值低及点燃点温度低,实际很少能够点燃。煤气回收限制性条件主要是防止回收爆炸性混合气体,它是安全进行煤气回收的基本条件。在确保有足够的煤气柜容量的条件下, 煤气回收的操作条件也是影响转炉煤气回收的主要因素。 煤气回收以烟气中的 CO 和 O2 含量为依据:CO 浓度不低于预定值,且 O2 浓度不高于预订值。 一般钢铁企业将该条件设置为 CO 不低于 30%,且 O2 不高于2%。 由于转炉煤气在正常吹炼的前期和后期CO往往低于30%,无法回收,需要对空放散,造成了环境污染与能源浪费,转炉喷煤技术则是利用高温喷煤,将烟气中CO2与C反应生成CO,提升CO浓度,提高转炉煤气的回收利用。向转炉内喷煤粉,冶炼全程回收煤气,利用炉内高温余热干馏煤粉,实现转炉冶炼低碳、绿色、环保多重效益。(2)转炉喷煤技术介绍 转炉煤气是钢铁企业重要的二次能源,占炼钢工序能源回收总量的80%~90%,转炉煤气主要用于冶金包烘烤、钢坯加热、化工产品生产和燃气发电等。 在转炉冶炼期间通过在转炉汽化烟道活动烟罩或移动段喷吹煤粉,在1000℃以上高温工况下使煤粉中的C与转炉烟气中的CO2发生还原反应,生成2mol的CO,既可以提高煤气回收时间、也可以提高回收煤气的热值。(3)经济效益
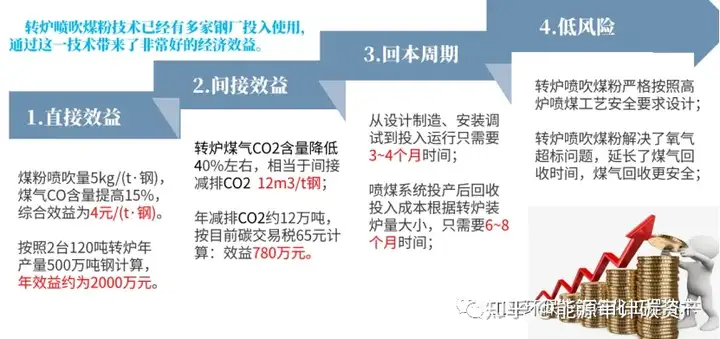

04低浓度瓦斯催化氧化及发电技术(1)技术背景:当瓦斯浓度低于8%时,低浓度瓦斯发电机不能有效利用,而直接排放到大气,不仅排放了大量温室气体,而浪费了宝贵的煤层气资源。催化燃烧方法可以在400℃以下将这些瓦斯完全燃烧,变成CO2和H2O,燃烧释放出的高温烟气(500-600℃)可以产生蒸汽,利用这些蒸汽发电,既能产生经济效益,又保护了环境。(2)技术原理 本技术采用计算机控制,对关键位置的温度、压力实时监控,并有完善的自动调节和联锁控制措施。发生催化氧化反应的催化剂床层温度控制在600℃以下,避免出现催化剂床层超温事故,保证装置的正常运行。 催化氧化是无焰燃烧,没有明火。装置排出的烟气温度低于100℃,装置的外壳有良好的保温措施,温度低于60℃,符合煤矿安全要求。 由于催化氧化技术可以利用浓度高于1.6%的瓦斯,故对低浓度瓦斯的浓度波动有很好的适应能力。不会因为浓度波动使催化氧化反应停止,造成装置停止运行。 催化氧化装置是本技术的核心设备。该装置将低浓度瓦斯氧化、余热锅炉、原料气余热、烟囱等均集成在一个装置上。与传统设计相比,提高了瓦斯氧化热量利用率20%,即蒸汽产量(发电量)提高了20%。同时,由于装置集成化程度高,节省了大量的占地,占地面积仅相当于传统设计的1/4,又可以降低制造成本、减少土建安装工程量。 经济效益好 由于催化氧化装置技术先进、效率高,使本技术的每MW投资与低浓度瓦斯发电的成本接近,投资回报期为2.5年左右。 本技术采用的催化剂寿命较长,使更换催化剂的费用占总运行费用的比例低于5%。
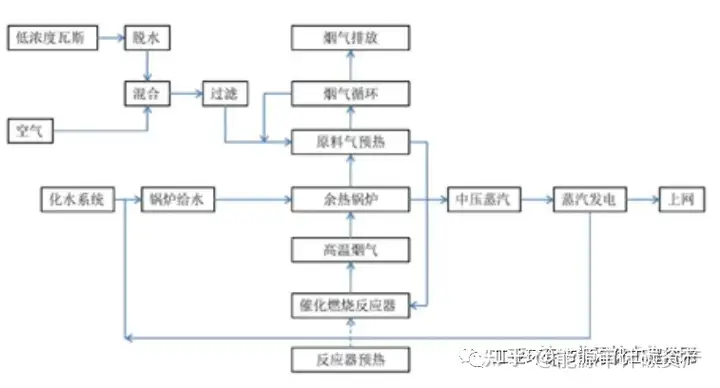

05电炉一次烟气全余热回收及除尘协同脱除二噁英技术(1)技术背景
电炉一次烟气具有烟气温度高(1400-1600℃)、粉尘浓度大(20-30g/Nm³)、粉尘粒度细、含有CO和二噁英等有害物质的特点。一直以来,电炉一次烟气存在二噁英排放浓度超标、烟气余热无法有效回收利用等问题,这就造成了炼钢成本居高不下、环境问题突出,在一定程度上也制约了我国短流程炼钢的推广和发展。 二噁英为剧毒、致癌物质,理化性质非常稳定,800℃以上才能氧化分解,同时250-500℃之间易在金属粉尘催化作用下发生从头合成反应重新生成,300℃以下多数转化为固态微细颗粒。鉴于二噁英以上特殊性质,目前电炉一次烟气多采用沉降室高温燃烧氧化分解、烟气急冷(降温速度>300℃/s,减少从头合成反应)、250-400℃喷入氨水抑制二噁英生成、混入电炉二次烟气稀释(电炉二次烟气量与一次烟气量之比约为10:1)、喷射活性炭吸附、布袋除尘器除尘(低温下二噁英约50%附着在除尘灰上被脱除,剩余穿过滤袋)等措施来控制二噁英排放。根据工程实际经验,采用以上多种措施组合,仍有很多电炉二噁英排放指标难以达标。同时,以上工艺流程复杂,且为抑制二噁英必须要对烟气进行急冷处理,这就导致烟气余热无法回收利用,增加了电炉的生产成本。(2)技术原理 从电炉第4孔/第2孔引出的1400-1600℃的电炉一次烟气,与调节活套处引入的空气混合后,直接进入燃烧沉降室充分燃烧,从而消耗掉烟气中的CO。燃烧沉降室出口烟气直接进入高温烟道式余热锅炉,充分回收利用烟气余热,将烟气温度直接降至180℃,然后进入除尘协同脱除二噁英装置,在除尘脱二噁英滤筒/滤袋的作用下,脱除粉尘并彻底催化分解二噁英,净化后烟气经引风机和烟囱最终达标排放。

所述除尘协同脱除二噁英装置,由除尘器本体、催化脱二噁英滤筒和输灰设备等组成,180℃烟气首先进入除尘器,在滤筒过滤作用下脱除烟气中的粉尘,催化脱二噁英滤筒是由超细玄武岩纤维复合脱二噁英催化剂制成,烟气中的二噁英在300℃以下多数以固态形式存在,但颗粒极细,大约50%左右粘附在除尘灰表面被脱除,剩余二噁英穿透滤筒表面进入滤筒催化层,在催化剂的催化作用下,彻底分解为H20、CO2和HCL等无机物,脱除粉尘和二噁英的净烟气通过滤筒进入除尘器净气室,最终经引风机和烟囱达标排放。02
余热高效利用技术

06低温吸收式制热机组(1)技术介绍
低温吸收式制热机组溴化锂驱动热源温度为35℃,其工作动力主要来源于工业废余热及一次供暖回水管网(50℃以下),我们定义为低温吸收式热泵制热机组。 这类吸收式制冷机组只需要用户利用工矿企业在生产过程中产生的必须排放的低温废热,即可实现溴化锂机组的运行和做功,形成用户需要的热。 经中国建筑科学研究院国家空调设备质量检验检测中心检测:热源水温度:40℃;使用侧出水温度49.5℃;转换效率:48%。(2)制热工作原理 主体由蒸发器、吸收器组成的上筒体,冷凝器、发生器组成的下筒体,溶液热交换器、溶液泵、冷剂泵、抽气系统等组成。制热机组工作时,主体处于真空状态。 发生器内溴化锂溶液受热浓缩为浓溶液,同时产生的冷媒蒸汽进入冷凝器,经冷却水冷却凝结成冷媒水,冷媒水被冷媒泵输送进入蒸发器,冷媒水在蒸发器内吸收传热管余热而蒸发,产生冷媒蒸汽进入吸收器;浓溶液经溶液泵输送,在热交换器吸收热量后进去吸收器,与来自发生器经换热器降温后的浓溶液吸收,浓溶液变稀溶液且温度升高,产生的吸收热被传热管的热水吸收。如此循环完成热水加热。(3)产品优势 制热最低只需35℃热源水,即可制取45℃(最高可制取50℃)热水供应冬季供暖。热源水温度越高,设备能效越高,制取冷冻水温度越低。 现有其他厂家的吸收式制热机组,基本都是大温差机组,无法进行低温转换;我司生产的低温吸收式制热机组,热源水需求温度40℃,转换效率48%。 将企业(电厂、化工厂、焦化厂、一次网回水等)生产过程中产生的大量40℃左右的工业余热水有效的利用起来,降低企业现有的生产成本,同时增加企业效益。(4)应用范围 低温吸收式制冷机组是一种以低温余废热或一次网回水作为热源,制取供暖水的节电型设备。它具有耗电少、噪声低、运行平稳、能量调节范围广、自动化程度高、安装、维护、操作简便等特点,在利用低势热能与余废热方面有显著的节能效果。 另外,它还有无环境污染、对大气臭氧层无破坏作用的独特优势。因而,制热机组被广泛应用于城市供暖等行业。
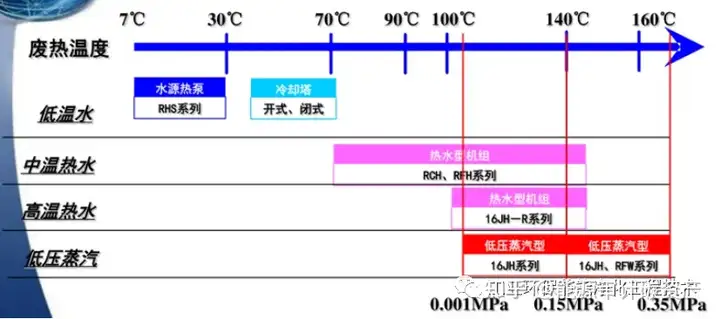

07低温吸收式制冷机组(1)技术介绍
低温吸收式制冷机组溴化锂驱动热源温度为65℃,其工作动力主要来源于工业废余热(70℃以下),我们定义为低温吸收式热泵制冷机组。这类吸收式制冷机组只需要用户利用工矿企业在生产过程中产生的必须排放的低温废热,即可实现溴化锂机组的运行和做功,形成用户年生产开关个数需要的冷。经中国建筑科学研究院国家空调设备质量检验检测中心检测:热源水温度:59.7℃;冷冻水出水温度6.4℃;转换效率:93%。(2)制冷工作原理主体由蒸发器、吸收器组成的下筒体,冷凝器、发生器组成的上筒体,溶液热交换器、溶液泵、冷剂泵、抽气系统等组成。制冷机工作时,主体处于真空状态。蒸发器内,低温冷剂水吸收来自用户的冷媒水的热量,使冷媒水温度降低;同时,冷剂水蒸发成冷剂蒸汽。吸收器内,溴化锂浓溶液吸收蒸发器内冷剂蒸汽后变成稀溶液。稀溶液在溶液泵的作用下,经过溶液热交换器的加热升温后,最后送至发生器内进行加热。发生器内,稀溶液通过高温热水的加热,成为高温浓溶液;同时产生大量的高温冷剂蒸汽。浓溶液经溶液热交换器与吸收器来的稀溶液换热后,进入吸收器。同时,产生的冷剂蒸汽进入冷凝器内被冷却,成为低温冷剂水。冷剂水经降压节流后进入蒸发器,这样就完成一个制冷循。
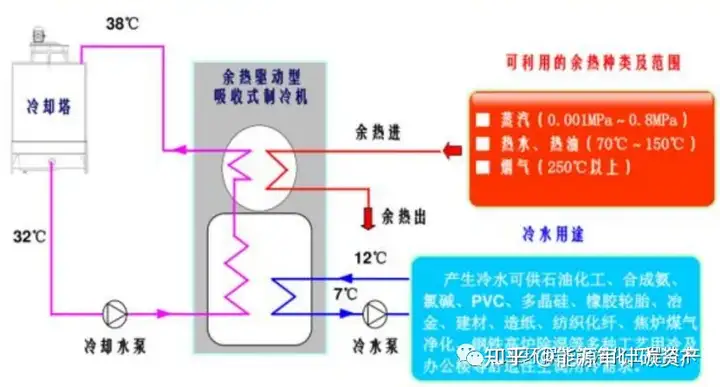
(3)产品优势 制冷最低只需65℃热源水,即可制取7-12℃(最低可制取2℃)冷冻水供应夏季制冷。热源水温度越高,设备能效越高,制取冷冻水温度越低。 现有其他厂家的吸收式制冷机组,热源水需求温度95-130℃,转换效率75%以内;我司生产的低温吸收式制冷机组,热源水需求温度60℃,转换效率93%。(4)应用范围 低温吸收式制冷机组是一种以低温余废热作为热源,制取冷水的节电型设备。它具有耗电少、噪声低、运行平稳、能量调节范围广、自动化程度高、安装、维护、操作简便等特点,在利用低势热能与余废热方面有显著的节能效果。 另外,它还有无环境污染、对大气臭氧层无破坏作用的独特优势。因而,被广泛应用于纺织、化工、医药、冶金、石化等行业。

08真空相变直热机组(1)技术背景
行业现状:在造纸、盐化工、煤化工、冶金等工业生产过程中,往往产生大量高温废水或循环水,如造纸行业的黑液、绿液,盐化工及煤化工的蒸氨废液、冶金行业的冲渣水等,该类废水中的热量往往不仅没有有效利用,甚至需要利用冷却塔散掉而消耗一部分电能。 技术难点:以上生产过程中产生的中高温工业废水,含有大量的杂质及各类无机盐,在换热过程中易发生结晶、结垢、腐蚀、堵塞换热器等问题,导致余热回收系统无法稳定运行而瘫痪,如何高效稳定地利用这部分热量是需要攻克的难点。

(2)技术原理 中高温工业废水进入罐体设备后,在负压环境下发生闪蒸,闪蒸出清洁水蒸气,清洁水蒸汽在冷凝器中换热得到清洁水,清洁水可提供工业热水、生活热水、建筑物供热等用途。在整个换热过程当中,废水闪蒸罐内没有换热面,不会产生结晶、结垢、腐蚀、堵塞换热器等问题,闪蒸出来是清洁乏汽,在之后的冷凝放热过程中不会对受热面产生污染,有效稳定地利用了这部分热量。
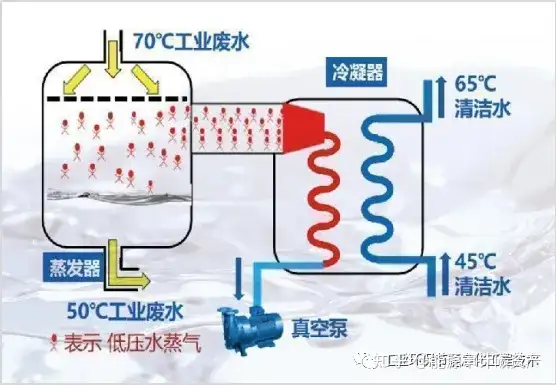
(3)适用范围 该产品广泛应用于化工、冶金、纺织、造纸等行业生产过程中产生的50℃以上的工业废水及工艺循环冷却水余热回收,将其热能转移至清洁水中,提供工业、生活热水或为建筑物供热。制热成本:3—10kW.h/GJ。

09有机朗肯循环低温余热发电技术(1)技术原理
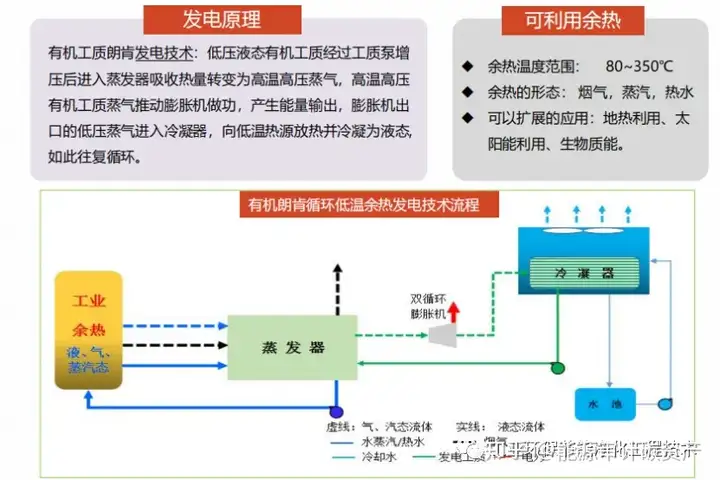
(2)应用范围
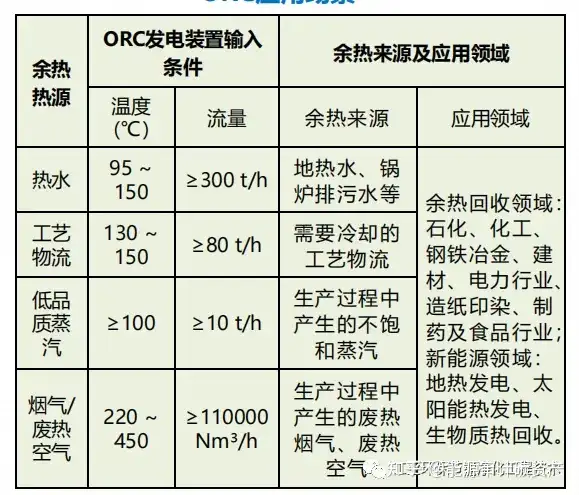

10螺杆膨胀机发电技术(1)技术原理
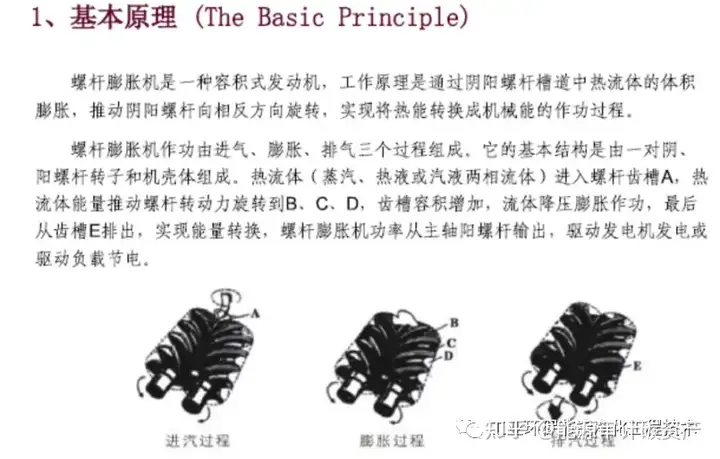
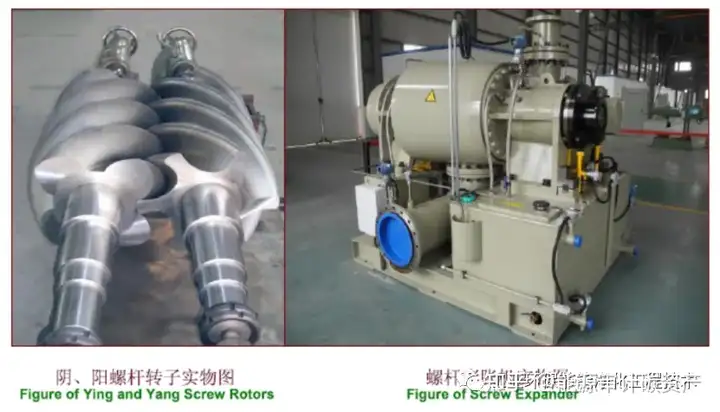
(2)技术特点
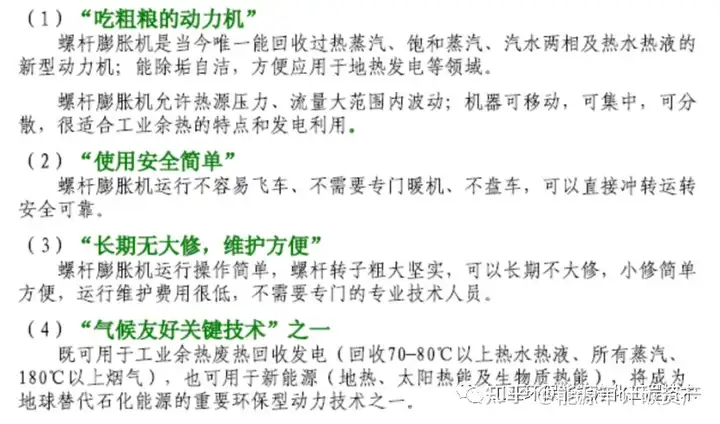
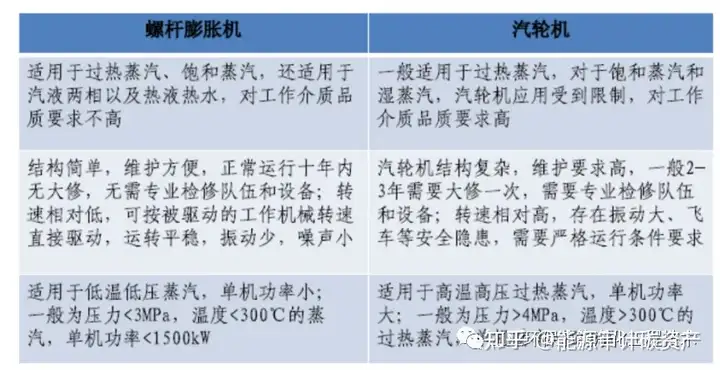
(3)螺杆膨胀机发电应用
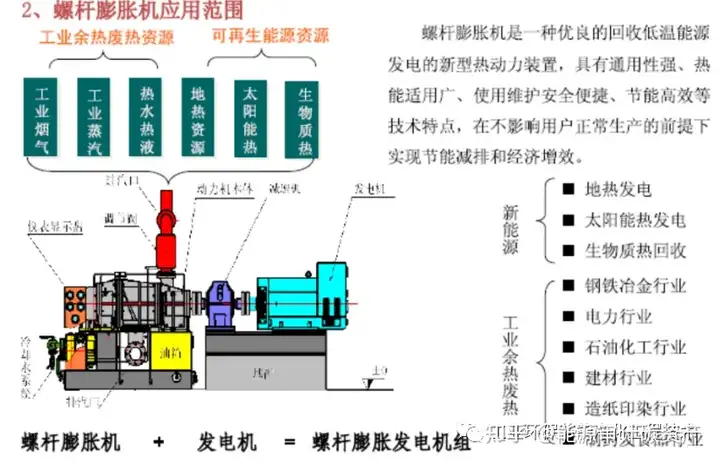
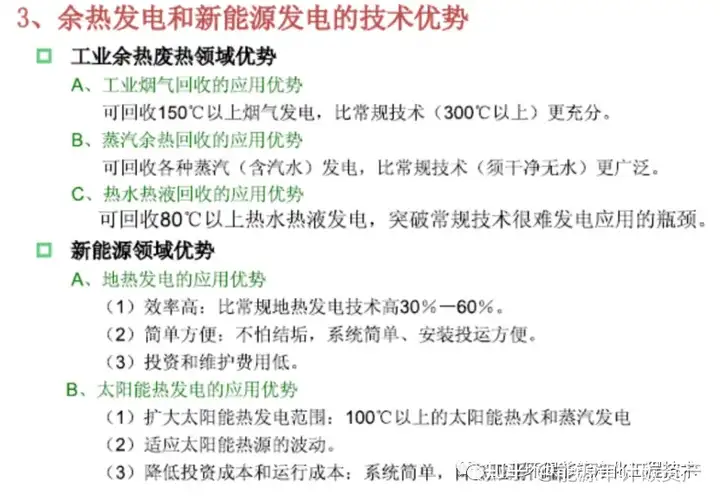
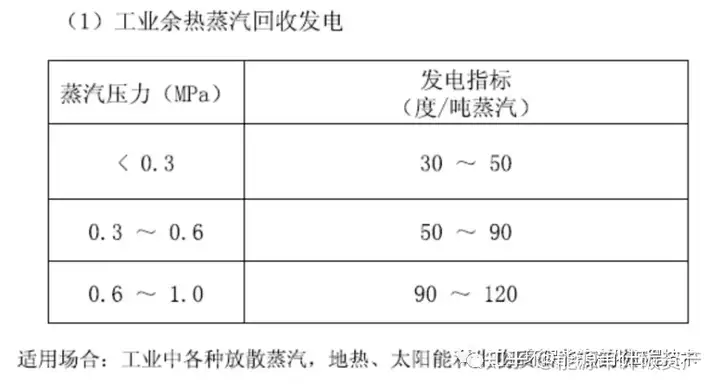
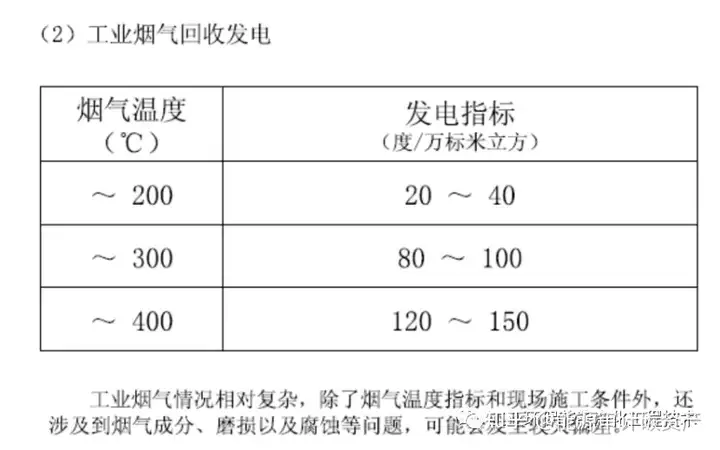
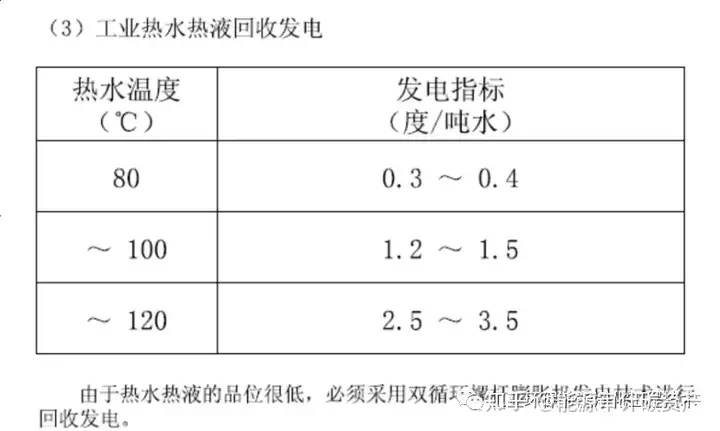